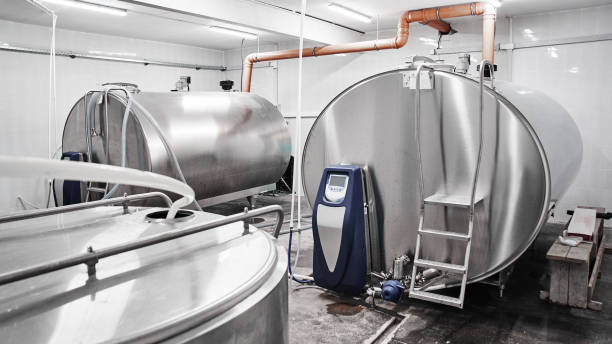
By Katie Spring, Outreach & Content Specialist at NE-DBIC
The Northeast Dairy Business Innovation Center (NE-DBIC), hosted at the Vermont Agency of Agriculture, Food & Markets, provides support to dairy businesses through projects that promote the development, production, marketing, and distribution of dairy products.
The Northeast Dairy Business Innovation Center is pleased to announce 23 recipients of the On-Farm Milk Storage & Handling Grant.
These funds allowed farmers to upgrade milk storage and handling, with most farms installing larger bulk tanks. The grant also funded other specialized equipment including plate coolers, glycol chillers, and pipeline systems. The larger bulk tanks allow many farmers to switch from daily milk pick-ups to every-other day, leading to savings on hauling costs, decreased fuel usage, and increased energy efficiency as older units are replaced with more efficient ones.
In one of the most competitive rounds we’ve seen, over 175 farms applied for the grant. With such a clear need for storage and handling funding across the region, NE-DBIC will be re-opening this grant again in fall of 2023.
Awards in this round ranged from $20,000- $50,000, with a total of $1,039,340 in overall funding.
On-Farm Milk Storage & Handling Grantees:
- Bedrock Farms of Vermont will install milk cooling and heat recovery systems to cool milk more quickly and efficiently, leading to increased milk quality and reduced farm energy costs.
- Bender Farms of Delaware will replace their current 2,000-gallon bulk tank with a 6,000-gallon bulk tank and install a new cooling system that will save energy on cooling and heating water. Together, these will allow them to ship milk every other day and save money on both hauling charges and energy costs.
- Blue Hill Farm of New York will replace one of their two bulk tanks with a 6,000-gallon bulk tank. This will allow them to switch to every-other day milk pickup, reducing energy costs, saving money on hauling stop charges, and increasing milk transfer efficiency.
- Brink Family Farm of New York will purchase and install a new 8,000-gallon bulk tank that will allow them to remain on every-other-day pickup following a consolidation of their milking operations into one barn, increase labor efficiency for the hauler and the farm, and allow for cost savings on energy and increased income from milk premiums.
- Conant Acres of Maine will install a 2,000-gallon bulk tank along with a plate cooler and new scroll condensing units, significantly reducing the energy costs of cooling milk, along with reducing labor and maximizing production.
- Lawtons Jersey Farm of New York will replace their current bulk tank with a new 2,000-gallon bulk tank along with new condensing units. This will allow them to ship milk every other day and save on hauler fees, energy, labor, and chemical usage.
- Lost Hollow Farm of Pennsylvania will replace their current bulk tank with a 4,000-gallon bulk tank along with a Fre-Heater system to recover heat from the milk cooling process to heat hot water for the farm. This will allow them enough storage to ship milk every other day and save on milk hauling costs, energy, and chemical usage.
- Maple Lawn Dairy of New York will replace their plate cooler with a new dual-port plate cooler and will replace their existing 2,000-gallon bulk tank with a new 8,000-gallon bulk tank. This will allow them to cool milk more efficiently and move to every-other day milk pickup, leading to savings on energy and stop fees.
- Maple Shade Farm of Massachusetts will replace their current water-cooled plate cooler with a new glycol chiller system. This will allow them to pre-chill raw milk more efficiently before it enters their bulk tank, thereby reducing costs associated with water usage.
- Meadow Ridge Farm of Connecticut will install a new plate cooler and water discharge reclamation system to pre-cool their milk more effectively, saving on energy costs and increasing milk quality.
- MK Dairy of New York will install a new 3,000-gallon bulk tank, replacing their cooling compressors and current cooling system with a plate cooler.
- Mystiq Heights of Vermont will replace a small buffer bulk tank with a 5,000-gallon bulk tank in order to create an automated two-tank system that will improve milk quality and efficiency and allow them to move to every-other-day milk pickup.
- Offhaus Farms of New York will install a new dual-stage plate cooler and chiller system to rapidly pre-cool their raw milk before it enters their bulk tanks, improving their cooling efficiency, increasing milk quality, and alleviating milk shipping delays.
- Raspberry Ridge Creamery of Pennsylvania will purchase and install a pipeline milking system on their sheep dairy to replace a bucket milking system, increasing labor efficiency and milk quality, and allowing them to increase production.
- Riss-Dale Farm of Pennsylvania will install a 5,000-gallon bulk tank to replace their undersized tank, as well as installing a plate cooler and variable speed transfer pump, allowing them to ship milk every other day rather than daily, increase milk quality, and reduce energy and milk hauling costs.
- Silver Maple Farm of Maine will replace their current 3,000-gallon tank with a new 6,700-gallon bulk tank. This will allow them enough storage to accommodate the production from a planned milking robot installation and have milk picked up every other day rather than daily.
- Stein Family Farms of New York will purchase and install a new plate cooler with glycol chiller to pre-cool their milk more efficiently and reduce reliance on their bulk tank cooling systems, which will allow them to save on energy costs, increase milk quality, and reduce instances of shipping delays due to inadequate cooling.
- Telaak Farms of New York will install a new 8,000-gallon bulk tank system and rapid load pump to enable milk pick up every other day rather than daily, improve milk quality, and increase energy efficiency.
- Tulip-Pond Farm of Maryland will install a larger bulk tank sized to allow their milk to be picked up every three days instead of daily, which will increase milk quality and farm cost savings in energy usage, labor, chemical supplies, and hauler fees.
- Up Over Acres of Pennsylvania will replace their two current bulk tanks with a 2,000-gallon bulk tank and a new cooling system. This will eliminate the need to move milk from one tank to the other and lead to energy and labor savings for the farm, increased milk quality, and reduced dumping of milk.
- Valley Hill Dairy of New York will purchase and install a new 8,000-gallon bulk tank with new scroll compressors. This will allow them enough storage to ship milk every other day and cool milk more efficiently, saving money on energy and increasing milk quality.
- William Haughwout of Pennsylvania will replace their undersized bulk tank with a 2,000-gallon tank, new compressors, and a system to reclaim heat from the bulk tank coolers, allowing the grantee to move to every-other-day milk pickup, reducing hauler charges, and increasing energy efficiency.
- Wil-Roc Farms of New York will Install a Piper AccuStream milk metering and in-line sampling system, which will eliminate inaccuracies in metering and component sampling and increase milk quality bonuses.